Your project team is probably familiar with the risks posed by delays. From paying extra for expedited shipping to missing out on favorable market conditions, any slip in an initiative’s timeline can have unwanted effects. But while you may already know about the most common financial costs of finishing a project late, facility startup efforts can bring some additional risks. And though some have direct costs tied to them, others create downstream problems that may not be obvious up front.
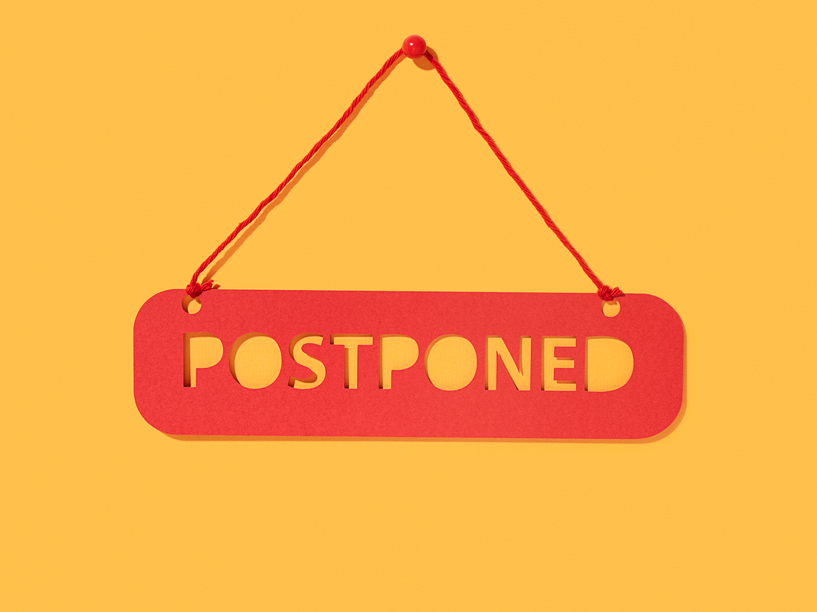
If you have a facility launch coming up, you need to be aware of the unique risks these projects carry. They have the potential to complicate your budget and even cause ripple effects far into the future.
1. Marketing efforts fall out of sync
Public announcements about new facility openings help to engage and build enthusiasm among community members, plus show customers and business partners how much the organization is growing. Some of these activities are planned a long time in advance, and a cascade of delays near the end of the project can throw the entire marketing strategy into disarray. Large-scale open house events, media opportunities, public tours—if they need to be postponed, your business may have trouble garnering good exposure and support when you’re finally ready to open your new site.
2. Staffing takes a hit
The addition of a new employer can be big news for the local job market. Even if your company already has a presence in the area, candidates anticipating an increase in employment opportunities will certainly be watching your project’s progress closely. When a facility startup initiative falls behind on the schedule, those key job seekers are likely to join other firms instead. By the time your facility finally comes online, attracting the right talent could be far more challenging.
3. Manufacturing workloads experience conflicts
If the new facility isn’t ready to deliver the expected amount of manufacturing capacity on time, the ripple effects can be significant. Either your existing facilities must continue to shoulder the load, or you may need to scale back on your production levels to fit other product lines into the schedule. This is particularly problematic if a current manufacturing line was expected to support a new product launch or other key strategic objective. And for businesses seeking to expand their production capabilities, the delay of the new facility could mean you aren’t able to fulfill rising order volumes.
4. Logistics and supply chain cost optimization plans suffer setbacks
Depending on where your new facility is located, your organization may have anticipated a drop in any number of operational expenses. Shipping rates could be cheaper to your new locale or warehousing costs in the vicinity might be lower. Any delay in putting those cost savings toward your bottom line could result in less money that’s available for other initiatives. It’s also possible that a lack of access to cost optimization options resulting from the delay of your new facility opening will require you to raise your product or service prices, potentially changing your revenue picture even further.
5. Funding options fade away
New facilities are typically investment-heavy endeavors, and many enterprises take advantage of external funding opportunities to help cover the costs. Tax breaks, grants, and cost-sharing arrangements often have sunset dates, and delays in your facility startup project could mean that you miss those important windows for financial support. Downstream funding might also evaporate if your new location falls behind schedule, including access to valuable research and development backing and even secondary initiatives such as solar credits, reduced pricing for public transportation partnerships, and other money-saving arrangements.
PMAlliance, Inc uses a team of highly experienced and certified professionals to provide project management consulting, project management training and project portfolio management.